OUR ENVIRONMENTAL SUSTAINABILITY JOURNEY SO FAR…
OUR ENVIRONMENTAL SUSTAINABILITY JOURNEY SO FAR…
2020
- Feasibility tests done on our steam boilers to replace heavy fuel oil by biofuel.
- Developed the first phase of our Eco-design project: a decisional tool to create and design sustainable products.
- Since August 2020, we committed to set science-based targets with the Science Based Targets initiative to reduce our emissions in line with climate science. We are the first company from the Textiles, Apparel & Luxury Goods sector based in the African region to commit to this bold initiative.
- Since September 2020, we became an official manufacturer member of the Sustainable Apparel Coalition (SAC)
2019
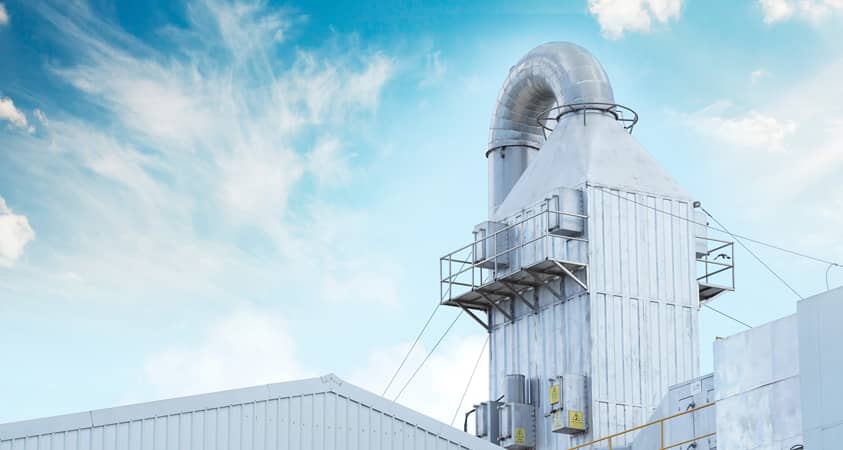
- Updating our long-term environmental strategy and environmental targets for 2025.
- Reviewing our environmental policy to reflect our long-term environmental strategy.
- Setting up our chemical policy.
- Since April 2019, we have been a registered user of the ZDHC Gateway and we disclose our wastewater results on the platform every 6 months.
- 80% less wastes are being sent to the landfill due to recycling and reuse of wastes.
- Setting up a chemical management system based on the Zero Discharge to Hazardous Chemicals (ZDHC) guidelines for safe and sustainable management of chemical use.
- Since December 2019, we became an official signatory of the Fashion Charter for Climate Action (UNFCCC) as part of our ambition to achieve net zero emissions.
- All hazardous wastes generated at RT Knits are being sent to the Interim Storage Facility for Hazardous Waste (ISFHW) located at La Chaumière.
- Installing an electrostatic precipitator but also a scouring equipment to remove presence of oil as mist in the stenters ’exhausts.
2018
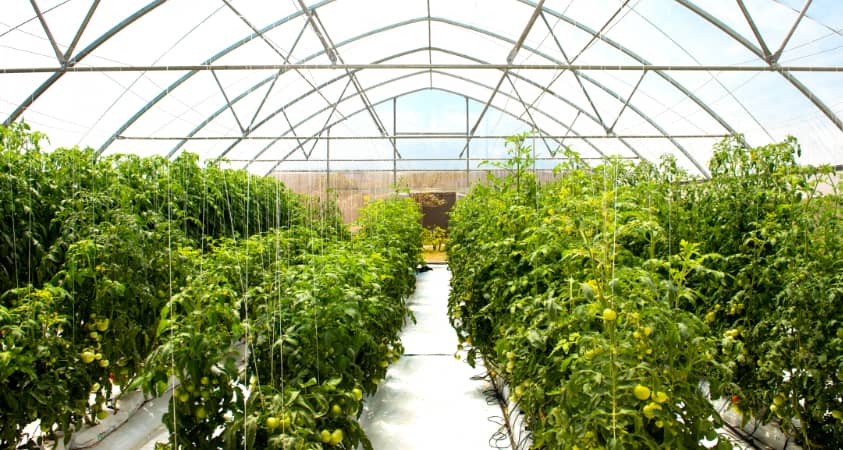
- Eco Olympics: Environmental campaign launched to promote pro-environmental behaviours among the RT family
- Hydroponics: A greenhouse was installed to promote sustainable and healthy agricultural practices among the RT family
- Centralisation of printing activities to La Tour Koenig which allowed for better utilities’ management
- Water from previous processes is reused in the dyehouse to cool machines instead of using fresh water.
- Natural ventilation for production floors (make up) instead of heavy-duty electrical ventilation equipment.
- Start sending our electronic wastes for safe disposal at a certified facility (Better waste management)
- Reduction of packaging wastes, e.g., we started purchasing yarns that are delivered in pallets instead of cartons.
- Creation of a dedicated EMS (Environmental Management System) team. An EMS leader was assigned to lead each priority area of RT EMS, i.e., energy, water, wastewater, air emissions, chemical management and solid wastes.
- We became a GOTS certified supplier for both fabrics and apparel.
- A greywater treatment plant was installed on the facility to treat greywater generated from dormitories. This treated water is reused for irrigation in the factory premises.
2017
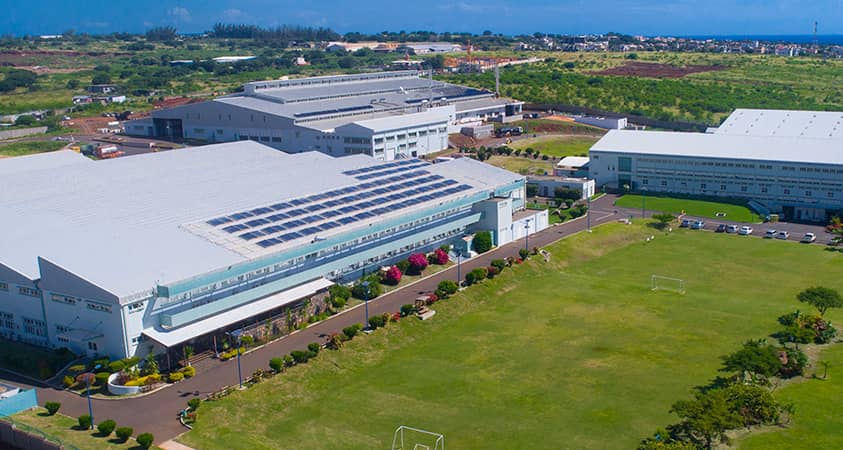
- Centralisation of all activities at La Tour Koenig
- Less vehicular emissions (30% reduction in diesel consumption) as a result of this centralisation.
- Automatic chemical dispensing for better chemical handling and management
- New steam boiler (Rotary cup) to improve efficiency and also reduce the number of particulates that are emitted. (3 times less Particulate Matter emitted)
- Heat recovery from stenter (186 L Heavy Fuel Oil (HFO) saved per day)
- Launching of RT EMS (environmental management system)
- Formulating the long-term environmental strategy
- Started using the HIGG INDEX tool to assess our sustainability performance
2016
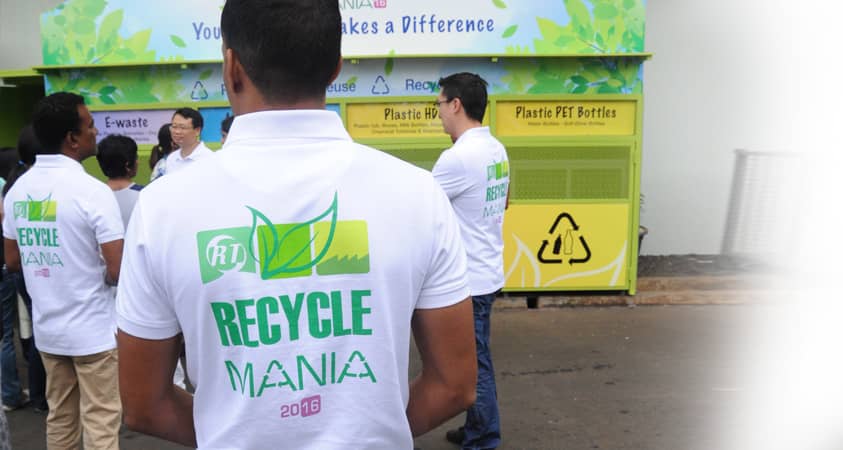
- Start replacing conventional fluorescent tubes by LED lighting
- Waste heat recovery from air compressor for hot water generation for washing process (4000 L HFO/year saved)
- Recycling campaign - Recycle mania (15 tonnes plastic, metal and e-wastes avoided from landfills)
- Biodiversity conservation: Creating an endemic corner to promote endemic plant species of the island. – Endemic corner
- Started working with Better Cotton Initiative (BCI) cotton
2015
Start leakage detection project to minimise water leaks across the factory premises
2014
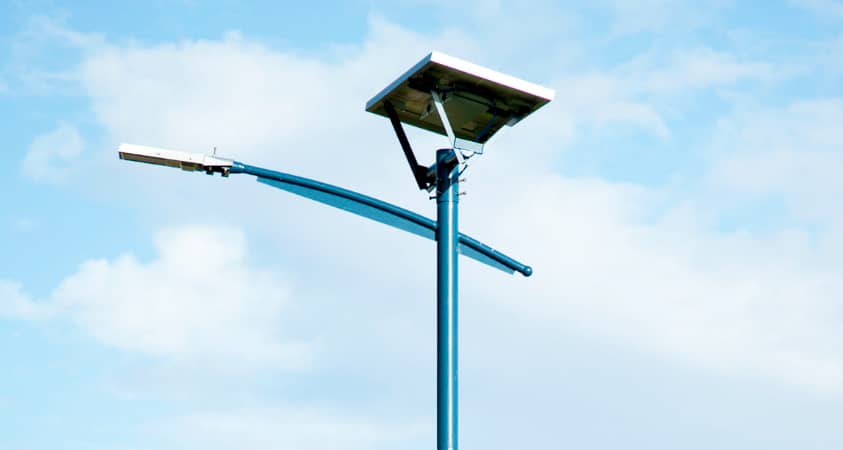
- Solar energy powered street lighting installed in factory premises
- Massive investment in low liquor ratio (LLR) dyeing machines (From 100L to 80L/kg dyed fabric)
2012
- Sustainable washing process: Sun wash (Ozone)
- Process optimisation for cold pigment dyeing (reduction of liquor ratio by up to 70%), Burn out (reduction of liquor ratio by up to 10%)
- Drip irrigation to reduce water for irrigation
Recover hot water from singeing (35 m3/day) at 75°C for reuse in dyeing
2011
- Hot water generation for garment wash process using solar water heaters (4000 L Diesel saved per year)
- Planting of endemic trees in factory premises
- 3R principle: waste management
Merging of Le Hochet and Beau Bassin to one entity:
- Process optimization for water and energy reduction, electricity and HFO reduction
- 30% reduction in water consumption
- Using unchlorinated water at Le Hochet (borehole) instead of chlorinated at Beau Bassin for dyeing
- Additional energy or chemicals was not required to treat the water before being supplied to the factory
2010
- Free distribution of solar water heaters to employees to promote use of renewable solar energy in sunny Mauritius.
- Reduction in water consumption in La Tour Koenig dormitory: Low flow showerhead and faucet aerators
2009
- Installation of VSDs and Servo drives in machineries and equipment (sewing machines)
2007 – 2008
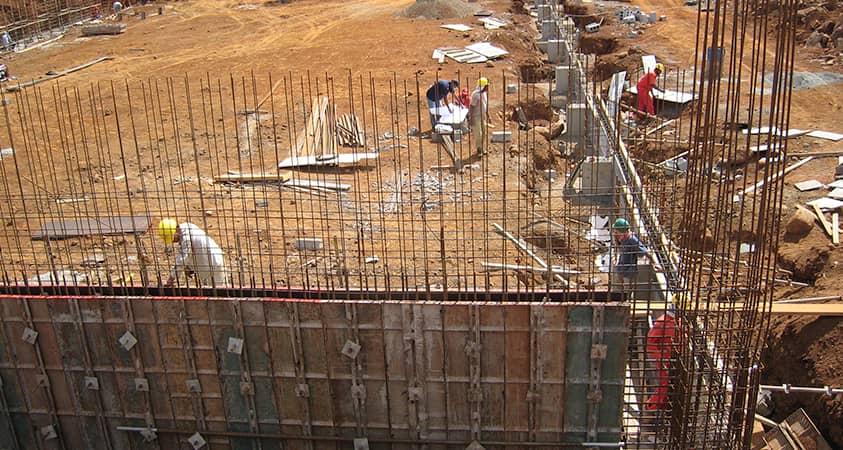
- Construction of new production site ta La Tour Koenig
- Building orientation to capture renewable energies namely, wind and solar energies (south light, South east trade wind).
- Building shape to smartly use of renewable energies.
- Natural lighting in make-up [80,000 kWh (80 tons CO2eq.) saved per year].
- Solar water heating for hot water generation in new dormitory at La Tour Koenig (15 tonnes LPG/year).
- Natural ventilation and extraction (200 kWh instead of 18,000 kWh per knitting machine).
- Yarn warehouse - Green building (13.4 kW installed, 45,000 kWh/year).
- Infiltration basins for rain water collection - Filtration membrane that goes to aquifers.
- Start sub metering all departments to better monitor utilities consumption.
- High efficiency compressor (15% more efficient motor).
- Preheating of feedwater for boiler using solar water heaters (Savings on diesel consumption, 4000L/year).
- Formulating the environmental and energy policies
2005 – 2006
- Start monitoring efficiency of boilers to reduce fuel consumption and consequently reduce our carbon footprint.
- Insulating hot fluids pipes for higher efficiency
- Rinsing and soaping in same bath to reduce water consumption
- Identifying opportunities for energy and water conservation including process optimisation.
- Heat recovery from wastewater effluent
*Although many small projects were undertaken, it was noted that due to a lack of space some projects could not be implemented. The management decided to centralise most activities to a new site namely, at La Tour Koenig for better efficiency and creating new avenues for innovation.